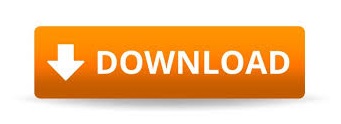

Nicholas makes a distinction between a shop that writes a technical estimate (all damage and parts uncovered and fully recorded on the estimate) and the shop that writes a sales estimate, their goal being to immediately capture the keys and uncover the hidden damage later. It may not be ideal for every shop, but in this case, it met the shop owner’s requirements. This design was for the smaller of two facilities a shop owner was building. Once all the fixed constraints are identified, Nicholas can begin to design a productive facility. All of those and many more immediately affect a shop’s layout and design.
#CAR BODY DESIGN CODE#
Environmental considerations like the retention basin for rainwater control and mandated green space meet legal code issues like traffic count, number of parking spaces required and the building’s position on the lot. The size of the lot, access to the roadway, utility routing, elevation, water drainage, curb cuts and numerous local regulations make each building site unique. Twelve-hour shifts, another crew, teams with overlapping work days or other facility use enhancements would be worth considering. If you now use your shop and equipment for a 40- to 45-hour work week, your expensive assets sit idle two-thirds of the time. As fixed costs to operate a profitable body shop increase steadily, using your invested capital wisely means more production, not more investment. One point Nicholas did make was that the cost to construct the facility can be recovered much more quickly if you utilize the building, equipment and technicians in more than one shift per day. Mark Thomas, National Training Manager, U-POL.Dan Reutter, Technical Specialist, U-POL.Cycle time reduction and increased throughput.Compatibility with other shop processes.
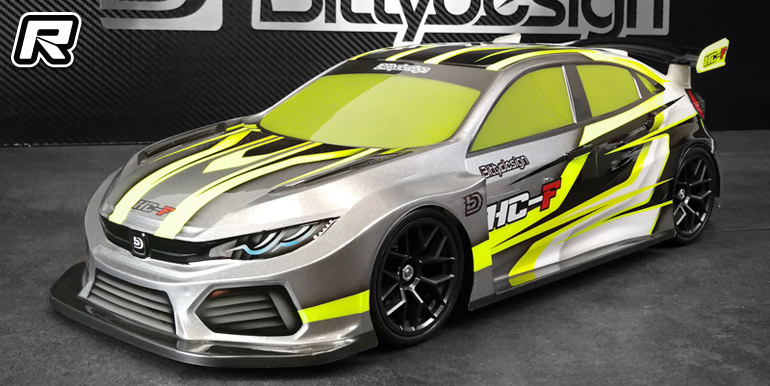


Due to its impressive portability, the HandySCAN 3D can perform the acquisition directly in the design studio but also on the customer's site, on a production floor or even in a small car body shop. Reverse engineering calls for the acquisition of dimensions on parts of various shapes and complexity, potentially performed in any kind of environment.
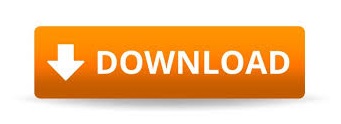